Today, customers expect warehouse operations to be more efficient and effective to provide competitive pricing and reduce errors. While the battle for efficiency is an endless race, logistics technology solutions like barcode scanners hold an essential place in meeting customer expectations.
In fact, the adoption of warehouse scanners is no longer seen as a nice-to-have solution but a must-have. Scanners have become a standard warehouse solution to increase efficiency and reduce errors across receiving, picking, shipping, and inventory operations.
According to Logistics MGMT, many logistics operations are turning to a range of automated data collection (ADC) technologies to increase efficiency and meet the growing demands of customers. The 2015 MHI Annual Industry Report exposes wearable and mobile technologies (including scanners) to no longer be emerging technologies but technologies that companies are rapidly adopting – in the “Growth” phase of the innovation adoption curve.
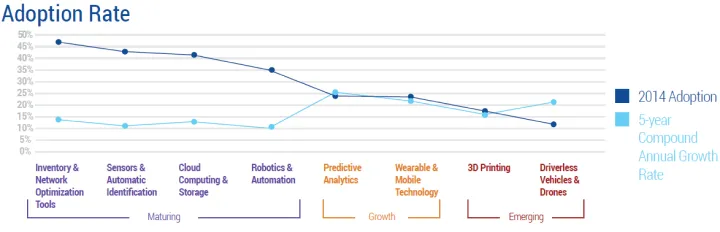
Source: 2015 MHI Annual Industry Report
Fewer Errors and More Speed
Warehouse scanners play a critical role in automating data collection in warehouse operations. They can read labels at light speed without errors.
On average, scanners have an accuracy of 1 error for every 70 million pieces of scanned information.
When properly integrated with a warehouse management system, this technology can reduce data entry to nearly zero and increase data collection speed across receiving, picking, shipping, and inventory management activities.
Quickly and accurately capturing information also increases the flow of information not only within the company but between the company and the customer. As items and cargo are scanned during order fulfillment, the captured information can be shared with customers or integrated systems.
In more technologically mature supply chains, automated processes like ordering can be initiated when the warehouse clerks scan an item for shipment and trigger an order volume threshold.
This extra level of visibility and automation across members of a supply chain can be a very powerful added value for companies to attract and retain large customers.
Increase Mobility and Efficiency
Following the natural evolution of technology, scanners have evolved from being physically attached to a terminal to becoming wireless capable devices. This means warehouse clerks no longer have to stand at a fixed location to scan items.
Having wireless barcode scanners increases warehouse efficiency by reducing unnecessary walking time. Although this might not be an obvious liability for smaller companies, as the business grows, this inefficiency starts to compound and, at some point, will result in preventable delays and unnecessary hires.
Wireless warehouse scanners are part of a larger mobile warehouse ecosystem that is beginning to shape the future of warehouse operations. Early adopters of mobility solutions in the warehouse will be the first ones to reap its benefits, delivering minimal errors and lowered costs to customers.
Capture More Information From Greater Distances
In the same way, that scanners have become mobile, they have also evolved in their ability to scan cargo from greater distances and capture more information.
It is not uncommon to see warehouse clerks struggle while trying to scan items that can’t be reached easily. Forklift operators are the most affected by this. When cargo is out of reach for the forklift operator’s barcode scanner, he/she needs to get off the forklift to scan the item and then get back on it. Long-range barcode solutions eliminate this.
Short-range warehouse barcode scanners can only scan items a few inches away. Long-range scanners can read barcodes from 25 to 70 feet away. With long-range scanners, forklift operators can scan cargo and items without having to get off the forklift.
As businesses continue to discover the benefits of big data and analytics, supply chain participants are increasingly requesting that their members capture and share more information. With 1D scanners, the ability to capture large amounts of information is inherently limited as they are only capable of capturing a limited amount, typically: location, product name, number, and a short description.
On the other hand, 2D scanners can capture larger amounts of information while occupying less packaging space. With 2D scanners, supply chain participants can now capture and share larger amounts of information that can later be analyzed to increase efficiency and make better-informed decisions.
So, if your goal is to increase the efficiency of warehouse operations, reduce errors, and/or capture more information, warehouse barcode scanners have a special place in achieving these goals. But even if none of these sound like a good enough reason to implement scanners, consider this: more and more businesses are making the switch, and at some point, your warehouse operations will not be as efficient as your competitors.
For more information about warehouse technology trends, you can follow us on LinkedIn, YouTube, X, or Facebook. If you have other inquiries or suggestions, please contact us here. We’ll be happy to hear from you.